Relokacja linii przemysłowych - Kluczowe kroki i wyzwania
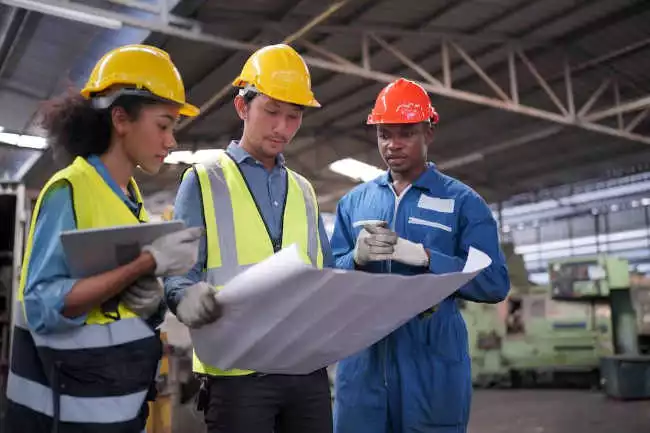
Relokacja maszyn przemysłowych i zakładów produkcyjnych to złożony proces, który wymaga starannego planowania i realizacji. W dzisiejszym artykule omówimy kluczowe kroki i wyzwania związane z relokacją maszyn i zakładów produkcyjnych. Dowiesz się, jakie czynniki trzeba wziąć pod uwagę, aby przeniesienie działalności przemysłowej odbyło się sprawnie i efektywnie.
Krok 1: Analiza i planowanie
Pierwszym krokiem w procesie relokacji jest dokładna analiza i planowanie. To tutaj określamy cele, terminy i budżet relokacji. Ważne jest również dokładne zrozumienie wszystkich procesów produkcyjnych oraz maszyn, które mają zostać przeniesione.
Określenie celów relokacji
W pierwszym etapie analizy i planowania, kluczowym zadaniem jest jednoznaczne określenie celów relokacji. Te cele stanowią fundament całego procesu i wyznaczają kierunek działań. Warto zadać sobie następujące pytania:
- Czy celem relokacji jest poprawa efektywności produkcji?
- Czy głównym celem jest redukcja kosztów produkcji?
- Czy relokujemy zakład produkcyjny ze względu na zmianę lokalizacji firmy?
- Czy możemy uzyskać dostęp do nowych rynków?
Jasno zdefiniowane cele pomogą w dalszej analizie i planowaniu, umożliwiając skoncentrowanie się na kluczowych aspektach relokacji.
Terminy i budżet
Ważnym elementem planowania relokacji jest określenie realistycznych terminów i budżetu. Terminy są szczególnie ważne, ponieważ zbyt krótka lub zbyt długa relokacja może prowadzić do niepotrzebnych komplikacji i kosztów.
- Określenie realistycznych terminów relokacji jest kluczowe. To moment, w którym musimy zastanowić się, ile czasu będzie potrzebne na przeprowadzenie wszystkich etapów procesu, w tym demontaż, transport, instalację oraz testy.
- Zdefiniowanie budżetu to kolejny kluczowy krok. Warto uwzględnić koszty związane z transportem, demontażem i instalacją maszyn, a także ewentualne koszty związane z przerwami w produkcji.
Należy pamiętać, że realistyczne oszacowanie terminów i budżetu to kluczowy element sukcesu całego projektu relokacji.
Krok 2: Wybór odpowiedniego partnera logistycznego
Relokacja maszyn i zakładów produkcyjnych to zadanie wymagające specjalistycznej wiedzy i doświadczenia. Wybór odpowiedniego partnera logistycznego jest kluczowy dla sukcesu operacji. Dowiedz się więcej na: http://dogged.pl/przenoszenie-maszyn-przemyslowych-i-zakladow-produkcyjnych.
Kryteria wyboru partnera logistycznego
Wybór partnera logistycznego to jedna z najważniejszych decyzji podczas procesu relokacji. Odpowiedni partner może znacząco wpłynąć na pomyślność całego przedsięwzięcia. Oto kluczowe kryteria, które warto wziąć pod uwagę przy wyborze partnera logistycznego:
1. Doświadczenie w relokacji maszyn przemysłowych
Najważniejszym kryterium jest doświadczenie partnera logistycznego w relokacji maszyn przemysłowych. Firma powinna posiadać udokumentowane przypadki udanych relokacji podobnych maszyn oraz zakładów produkcyjnych. Doświadczenie to gwarantuje, że partner rozumie specyfikę procesu relokacji i potencjalne wyzwania.
2. Sprzęt i zasoby umożliwiające przewóz ciężkich maszyn
Transport maszyn przemysłowych, zwłaszcza tych ciężkich, wymaga specjalistycznego sprzętu i odpowiednich zasobów. Partner logistyczny powinien dysponować odpowiednimi pojazdami, dźwigami, oraz innym niezbędnym wyposażeniem do bezpiecznego przewozu i manipulacji maszynami. Upewnij się, że firma posiada odpowiednią infrastrukturę, aby sprostać wymaganiom relokacji.
3. Referencje od innych firm, które korzystały z ich usług
Przed podjęciem decyzji o wyborze partnera logistycznego warto zasięgnąć opinii od innych firm, które korzystały z usług danej firmy logistycznej. Referencje i opinie od klientów są cennym źródłem informacji na temat jakości usług, terminowości oraz profesjonalizmu partnera. Sprawdzenie referencji pomoże uniknąć potencjalnych niespodzianek i zagwarantuje, że partner jest godny zaufania.
Podsumowując, wybór partnera logistycznego to kluczowy krok w procesie relokacji maszyn i zakładów produkcyjnych. Kierując się kryteriami doświadczenia, dostępu do specjalistycznego sprzętu i pozytywnymi referencjami, można zwiększyć szanse na skuteczną i bezproblemową relokację.
Krok 4: Transport i instalacja
Gdy maszyny są już gotowe do przewozu, czas na ich transport i instalację w nowej lokalizacji. To etap, który wymaga precyzji i staranności, aby zapewnić bezpieczne przeniesienie i sprawne uruchomienie maszyn.
Transport maszyn
Transport maszyn to jeden z kluczowych etapów relokacji. Wybór odpowiednich środków transportu oraz monitorowanie bezpieczeństwa maszyn podczas przewozu są niezwykle istotne.
1. Wybór odpowiednich środków transportu
Przy wyborze środków transportu należy wziąć pod uwagę rozmiar, waga oraz rodzaj maszyn. Dla mniejszych maszyn mogą być wystarczające standardowe pojazdy, ale w przypadku dużych i ciężkich urządzeń może być konieczne zastosowanie specjalistycznych środków, takich jak niskopodwoziowe przyczepy czy dźwigi. Wybór odpowiedniego transportu zapewni bezpieczny przewóz maszyn.
2. Monitorowanie bezpieczeństwa maszyn podczas transportu
Bezpieczeństwo maszyn podczas transportu to priorytet. Należy regularnie monitorować stan maszyn, aby upewnić się, że nie dochodzi do uszkodzeń w trakcie przewozu. Odpowiednie zabezpieczenia, takie jak specjalne uchwyty czy poduszki amortyzujące, mogą być niezbędne, aby zapewnić stabilność i bezpieczeństwo podczas transportu.
Instalacja maszyn
Po dotarciu maszyn do nowej lokalizacji, następnym krokiem jest ich instalacja. Montaż maszyn w nowym miejscu zgodnie z dokumentacją techniczną jest niezwykle istotny, aby zapewnić ich prawidłowe funkcjonowanie.
1. Montaż maszyn
Montaż maszyn to proces, który wymaga precyzji i dokładności. Pracownicy odpowiedzialni za montaż powinni działać zgodnie z dokumentacją techniczną maszyn oraz stosować się do określonych procedur. Każdy element maszyny, od elektrycznych po mechaniczne, musi być właściwie zamontowany, aby maszyna działała efektywnie i bezpiecznie.
2. Testowanie i uruchamianie maszyn
Po montażu maszyn przeprowadza się testowanie i uruchamianie. To etap, w którym sprawdza się, czy maszyny działają poprawnie i zgodnie z oczekiwaniami. Testy mogą obejmować sprawdzenie parametrów technicznych, kalibrację oraz eliminację ewentualnych usterek. Dopiero po udanych testach maszyny są gotowe do pełnej produkcji.
Podsumowując, transport i instalacja maszyn to kluczowy etap procesu relokacji. Wybór odpowiednich środków transportu, dbałość o bezpieczeństwo maszyn podczas transportu, a także dokładny montaż i testowanie to kluczowe elementy zapewniające sukces relokacji.
Krok 5: Kontrola jakości i optymalizacja procesów
Po zakończeniu relokacji ważne jest, aby dokładnie przetestować wszystkie maszyny i procesy produkcyjne. To etap, w którym dbamy o to, aby nowa lokalizacja sprawnie funkcjonowała i spełniała wszystkie oczekiwania.
Kontrola jakości
Kontrola jakości to nieodłączna część procesu relokacji, mająca na celu zapewnienie, że produkty wytwarzane po przeniesieniu są nadal zgodne z wymaganiami jakościowymi.
1. Badanie jakości produktów po relokacji
Po uruchomieniu maszyn w nowej lokalizacji należy przeprowadzić dokładne badanie jakości produkowanych wyrobów. Porównuje się je z wcześniejszymi normami jakości, aby upewnić się, że jakość produktów nie uległa pogorszeniu. Warto także zbadać ewentualne zmiany w parametrach procesu produkcyjnego, które mogą wpłynąć na jakość produktów.
2. Usuwanie ewentualnych usterek i problemów
W trakcie kontroli jakości mogą pojawić się usterek lub problemy. W takim przypadku konieczne jest natychmiastowe działanie w celu ich usunięcia. To etap, w którym doświadczony personel techniczny przeprowadza diagnozę i naprawia wszelkie usterki, aby zapewnić ciągłość produkcji.
Optymalizacja procesów
Optymalizacja procesów produkcyjnych to kluczowy element sukcesu w nowej lokalizacji. Warto stale monitorować i doskonalić procesy, aby osiągnąć jak najlepszą wydajność i efektywność.
1. Monitorowanie efektywności procesów produkcyjnych
Po relokacji maszyn i zakładów produkcyjnych ważne jest regularne monitorowanie efektywności procesów produkcyjnych. To oznacza zbieranie danych, analizę wskaźników wydajności oraz identyfikowanie ewentualnych obszarów, które wymagają poprawy. Monitorowanie efektywności pozwala na szybkie reagowanie na ewentualne problemy i ograniczenie przestojów produkcyjnych.
2. Wprowadzanie ewentualnych ulepszeń i optymalizacji
Na podstawie monitoringu efektywności procesów produkcyjnych można wprowadzać ewentualne ulepszenia i optymalizacje. To moment, w którym można doskonalić ustawienia maszyn, procedury pracy oraz organizację produkcji. Wprowadzenie innowacji może prowadzić do zwiększenia wydajności i redukcji kosztów produkcji.
Podsumowując, kontrola jakości i optymalizacja procesów to kluczowy etap po relokacji maszyn i zakładów produkcyjnych. Regularna kontrola jakości i ciągłe doskonalenie procesów gwarantują, że nowa lokalizacja będzie sprawnie funkcjonować i przynosić oczekiwane korzyści.
Krok 6: Dokumentacja i szkolenie personelu
Ostatnim etapem relokacji jest dokładne udokumentowanie wszystkich zmian oraz szkolenie personelu w obszarze obsługi nowych maszyn i procesów produkcyjnych. Zapewnia to, że po relokacji firma będzie działać sprawnie i efektywnie, a personel będzie przygotowany do obsługi nowych technologii.
Dokumentacja
Dokumentacja to kluczowy element procesu relokacji, który pozwala na zachowanie pełnej przejrzystości i umożliwia efektywne zarządzanie nową lokalizacją.
1. Sporządzenie raportów i dokumentów związanych z relokacją
Należy sporządzić szczegółowe raporty i dokumenty związane z całym procesem relokacji. Raporty te powinny zawierać informacje o krokach podejmowanych na każdym etapie, w tym o celach, planach, kosztach oraz ewentualnych problemach napotkanych w trakcie relokacji. Dokumentacja ta jest cennym źródłem informacji dla kierownictwa oraz może być przydatna w przyszłości przy ewentualnych relokacjach lub modyfikacjach procesów.
2. Archiwizacja danych związanych z procesem relokacji
Zarchiwizowanie danych związanych z procesem relokacji jest istotne ze względu na potrzebę zachowania historii działań firmy. Warto przechowywać dokumenty, rysunki techniczne, umowy oraz wszelkie informacje związane z relokacją. To pozwoli na zachowanie pełnej traceability procesu i ułatwi ewentualne audyty czy analizy.
Szkolenie personelu
Szkolenie personelu to kluczowy element zapewnienia płynnej adaptacji do nowych warunków i technologii w nowej lokalizacji.
1. Przeszkolenie pracowników w zakresie obsługi nowych maszyn
Przeszkolenie pracowników w obszarze obsługi nowych maszyn jest niezbędne, aby zapewnić, że będą w stanie korzystać z urządzeń w sposób efektywny i bezpieczny. Szkolenia powinny być dostosowane do specyfiki maszyn oraz potrzeb pracowników. Dla operatorów maszyn istotne jest poznanie procedur obsługi i bezpieczeństwa, podczas gdy personel techniczny powinien otrzymać szkolenia z zakresu konserwacji i napraw.
2. Zapewnienie wsparcia technicznego w okresie adaptacji
Po relokacji ważne jest, aby zapewnić personelowi odpowiednie wsparcie techniczne w okresie adaptacji. Może to obejmować stałą dostępność serwisu technicznego lub możliwość szybkiego uzyskania pomocy w razie awarii lub problemów. Dobre wsparcie techniczne pozwoli zminimalizować przestoje produkcyjne i zapewni bezpieczeństwo pracy.
Podsumowując, dokładna dokumentacja i skuteczne szkolenie personelu są nieodzowne po zakończeniu relokacji. Dzięki nim firma może sprawnie funkcjonować w nowej lokalizacji, a personel będzie gotowy do efektywnej obsługi nowych maszyn i procesów produkcyjnych.
Relokacja maszyn przemysłowych i zakładów produkcyjnych to skomplikowany proces, który wymaga precyzyjnego planowania i realizacji. Kluczowymi krokami są analiza i planowanie, wybór odpowiedniego partnera logistycznego, demontaż i przygotowanie maszyn, transport i instalacja, kontrola jakości i optymalizacja procesów, a także dokładna dokumentacja i szkolenie personelu. Tylko odpowiednie podejście i staranność pozwolą na skuteczną relokację i uniknięcie potencjalnych problemów.