Małe zmiany, duży efekt – skuteczne metody usprawniania procesów produkcyjnych
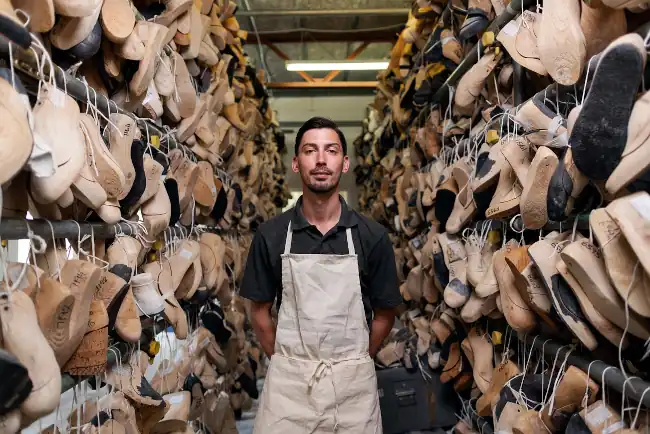
Optymalizacja procesów produkcyjnych – małe zmiany, wielki efekt
W świecie przemysłu, gdzie każda sekunda i każdy centymetr przestrzeni mają znaczenie, optymalizacja procesów produkcyjnych staje się kluczowym elementem strategii rozwoju wielu firm. Niezależnie od branży, przedsiębiorstwa dążą do zwiększenia wydajności, ograniczenia kosztów i poprawy jakości. I choć często skupiamy się na spektakularnych innowacjach, to w praktyce to właśnie drobne, systematyczne usprawnienia przynoszą największe i najbardziej trwałe rezultaty.
Co naprawdę oznacza „optymalizacja”?
Optymalizacja nie polega wyłącznie na wdrażaniu drogich systemów automatyzacji czy robotyzacji. To przede wszystkim umiejętność krytycznego spojrzenia na bieżące procesy i znalezienie obszarów, w których można coś zrobić lepiej, szybciej lub taniej – bez kompromisów w kwestii jakości.
Czasem wystarczy przeorganizowanie stanowiska pracy, skrócenie trasy transportu wewnętrznego, zmiana kolejności operacji lub lepsze rozmieszczenie maszyn. Nawet drobne zmiany, które skracają proces o kilka sekund, w skali miesiąca lub roku przekładają się na znaczące oszczędności.
Lean Manufacturing – filozofia ciągłego doskonalenia
Wielu menedżerów produkcji inspiruje się zasadami Lean Manufacturing, czyli koncepcji zarządzania produkcją pochodzącej z Japonii. Jej głównym celem jest eliminacja marnotrawstwa (jap. muda) – czyli wszelkich działań, które nie przynoszą wartości dodanej z punktu widzenia klienta.
Zgodnie z filozofią lean, warto nieustannie zadawać pytania: czy dana czynność jest konieczna? Czy da się ją uprościć? Czy materiał lub półprodukt nie przemieszcza się zbyt daleko? Czy operator nie wykonuje zbędnych ruchów?
Odpowiedzi na te pytania prowadzą często do bardzo praktycznych rozwiązań: wdrożenia systemu 5S, zmiany organizacji linii montażowej, czy zastąpienia ręcznego przenoszenia elementów bardziej ergonomicznymi metodami.
Przemysł 4.0 – cyfrowa transformacja produkcji
W ostatnich latach coraz większy wpływ na optymalizację procesów ma tzw. czwarta rewolucja przemysłowa, czyli Przemysł 4.0. To trend oparty na integracji technologii cyfrowych z tradycyjnym środowiskiem produkcyjnym. Kluczową rolę odgrywają tu: Internet Rzeczy (IoT), analiza danych w czasie rzeczywistym, uczenie maszynowe oraz automatyka.
Dzięki cyfrowym bliźniakom (digital twins), fabryki mogą dziś testować zmiany w wirtualnym środowisku, zanim zostaną one wdrożone fizycznie. Czujniki monitorujące temperaturę, zużycie energii czy pracę silników pozwalają szybciej identyfikować problemy i minimalizować przestoje.
Jednak, mimo zaawansowania technologii, to właśnie umiejętność połączenia narzędzi cyfrowych z praktyką i doświadczeniem ludzi stanowi największy potencjał przemysłu przyszłości.
Usprawnienia mechaniczne – praktyczna strona efektywności
Nie wszystkie procesy wymagają pełnej automatyzacji. W wielu zakładach przemysłowych i centrach logistycznych dużą rolę odgrywają sprawdzone rozwiązania mechaniczne, które są proste, niezawodne i relatywnie tanie w utrzymaniu.
Jednym z przykładów są systemy przenośników grawitacyjnych, wykorzystywane do transportu towarów bez konieczności użycia zasilania. Dzięki odpowiedniemu nachyleniu i właściwie dobranym komponentom, takim jak rolki grawitacyjne, możliwe jest płynne i bezpieczne przesuwanie paczek, kartonów czy pojemników wzdłuż linii. Takie rozwiązania są szczególnie popularne w obszarach sortowania, pakowania oraz przy odbiorze produktów z maszyn.
Ich zaletą jest nie tylko prostota, ale także niski koszt eksploatacji i łatwość integracji z innymi systemami. W połączeniu z ręcznym lub półautomatycznym systemem pracy stanowią świetne narzędzie do usprawniania przepływu materiałów.
Kultura organizacyjna jako podstawa sukcesu
Optymalizacja to nie tylko sprzęt i technologia, ale też – a może przede wszystkim – ludzie. Najlepsze rezultaty osiągają te firmy, które angażują swoich pracowników w procesy doskonalenia. Operatorzy maszyn, technicy, magazynierzy – to oni najlepiej znają problemy codziennej pracy i często mają najciekawsze pomysły na ich rozwiązanie.
Warto więc tworzyć kulturę otwartości, w której każda sugestia ma znaczenie, a inicjatywa jest nagradzana. Regularne audyty wewnętrzne, tablice Kaizen, czy spotkania zespołów produkcyjnych to narzędzia, które pomagają utrzymać wysoki poziom zaangażowania i ciągłego rozwoju.
Podsumowanie
W świecie nowoczesnej produkcji nie ma miejsca na stagnację. Firmy, które chcą być konkurencyjne, muszą stale szukać sposobów na poprawę – zarówno w skali makro, jak i mikro. Czasem będzie to inwestycja w nową linię technologiczną, innym razem wystarczy zmiana organizacji stanowiska pracy lub zastosowanie prostego, lecz efektywnego rozwiązania.
Prawdziwa siła optymalizacji tkwi w świadomości, że doskonalenie to proces, a nie jednorazowe działanie. I że nawet najmniejsza zmiana – jeśli jest dobrze przemyślana – może przynieść wielką różnicę.