Druk 3D a tulejki redukcyjne – czy można je wydrukować i czy to w ogóle działa?
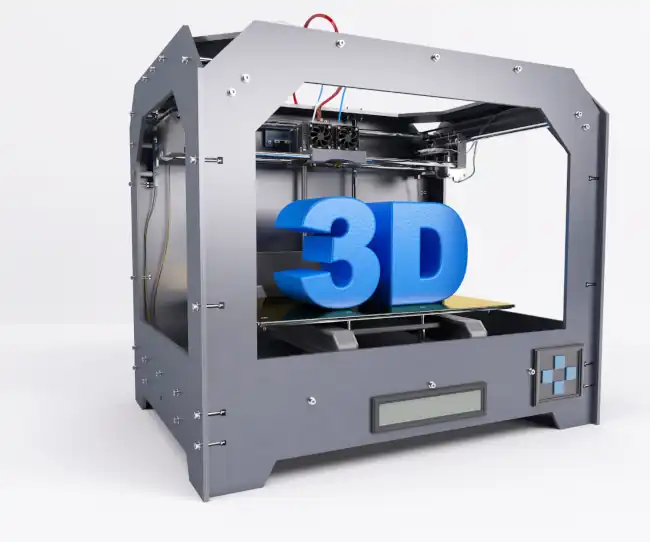
Dynamiczny rozwój technologii druku 3D otworzył wiele możliwości w różnych branżach. Drukowane elementy sprawdzają się w prototypowaniu i tworzeniu części zamiennych oraz niestandardowych komponentów. Nic więc dziwnego, że pojawia się pytanie, czy tulejki redukcyjne również mogą być produkowane w ten sposób. Czy wydrukowane tulejki spełnią swoją funkcję? Jakie materiały można wykorzystać? A może klasyczne, precyzyjnie wykonane tuleje nadal pozostają bezkonkurencyjne? Sprawdzamy!
Jakie wymagania muszą spełniać tulejki redukcyjne?
Tulejki redukcyjne to niewielkie, jednak niezwykle istotne elementy konstrukcyjne wielu sprzętów. Ich zadaniami są dopasowanie średnicy wałka do większego otworu, stabilizacja połączenia i ochrona elementów przed nadmiernym zużyciem. Aby spełniały swoją funkcję, muszą wyróżniać się:
-
wysoką odpornością mechaniczną,
-
precyzyjnymi wymiarami,
-
niskim współczynnikiem tarcia,
-
odpornością na wysokie temperatury i środki chemiczne.
Standardowo tulejki wykonuje się z metalu, kompozytów lub tworzyw sztucznych o podwyższonej wytrzymałości. Czy druk 3D pozwala uzyskać równie trwały produkt?
Jakie materiały można wykorzystać w druku 3D?
Wydruk tulejki redukcyjnej jest technicznie możliwy, jednak warto mieć na uwadze, że jego trwałość zależy od wybranego materiału. Drukarki 3D obsługują różne filamenty. Niestety większość z nich nie zapewnia wystarczającej wytrzymałości. Najczęściej stosowane materiały to:
-
PLA – łatwy w druku, ale mało odporny na obciążenia mechaniczne i temperatury powyżej 60°C.
-
ABS – lepsza wytrzymałość mechaniczna niż PLA, ale nadal nie dorównuje tulejom metalowym ].
-
Nylon – wytrzymały i odporny na ścieranie, jednak wymaga bardzo precyzyjnych ustawień drukarki.
-
PET-G – odporny na wilgoć i chemikalia, niemniej pod dużym naciskiem może się deformować.
-
Kompozyty wzmocnione włóknem węglowym lub szklanym – jedna z najlepszych opcji, ale nadal nie osiąga parametrów metalu.
W teorii można wydrukować tulejki redukcyjne z bardziej zaawansowanych tworzyw, jednak w praktyce ich odporność na ścieranie i precyzja wykonania często pozostawiają wiele do życzenia.
Problemy z drukowanymi tulejkami redukcyjnymi
Chociaż druk 3D daje dużą swobodę w tworzeniu niestandardowych kształtów, nie zawsze sprawdzi się w przypadku elementów poddawanych intensywnym obciążeniom. Do największych problemów z drukowanymi tulejkami należą:
-
Brak idealnej gładkości – powierzchnia druku warstwowego nie jest tak precyzyjna jak w przypadku obróbki skrawaniem.
-
Słabsza odporność na tarcie – nawet nylon czy PET-G zużywają się szybciej niż metal.
-
Niższa odporność termiczna – większość filamentów ulega deformacji przy wysokich temperaturach.
-
Konieczność wielokrotnego testowania – wydrukowana tulejka może wymagać wielu prób, zanim spełni swoje zadanie.
Druk 3D jako alternatywa czy tylko rozwiązanie awaryjne?
Podsumowując, tulejki redukcyjne wykonane w technologii druku 3D mogą stanowić rozwiązanie tymczasowe lub być stosowane w prototypowaniu. Jednak trudno im konkurować z klasycznymi modelami dostępnymi na rynku. W zastosowaniach wymagających wysokiej precyzji i odporności lepiej postawić na sprawdzone, trwałe tulejki wykonane metodami tradycyjnymi.